Top Reasons to Choose Professional Welding Inspection Milwaukee Services
A Comprehensive Guide to Welding Inspection Techniques and Ideal Practices for Quality Control in Manufacture Projects
Welding assessment works as a basic column in guaranteeing the structural stability and safety and security of fabricated jobs. Using a variety of strategies-- ranging from aesthetic evaluations to sophisticated approaches like ultrasonic and radiographic testing-- offers crucial insights right into potential flaws that might undermine toughness. Developing reliable techniques and a durable high quality monitoring system can enhance compliance and reliability. The ins and outs of these techniques and their execution commonly raise essential concerns concerning the standards and devices necessary for optimum outcomes. What particular methodologies will be most reliable in your projects?
Value of Welding Examination
Welding assessment is a critical part in ensuring the honesty and security of welded frameworks. The procedure includes an organized analysis of welds to identify any type of flaws that might jeopardize the strength and resilience of the end product. Reliable assessment is necessary not just for compliance with market standards and regulations however likewise for safeguarding the health and wellness of employees and the public.

Additionally, welding examination offers as an important tool for continuous improvement in construction processes. Ultimately, prioritizing welding inspection fosters a society of top quality guarantee, making sure that jobs meet both customer assumptions and governing needs.
Typical Welding Evaluation Methods
Numerous strategies are used to check welds, each tailored to identify particular sorts of flaws and guarantee quality. Among one of the most typically utilized approaches are visual inspection, ultrasonic screening, radiographic screening, magnetic particle testing, and dye penetrant testing.
Visual inspection is one of the most straightforward technique, allowing assessors to identify surface abnormalities such as cracks, porosity, and undercutting. Ultrasonic testing uses high-frequency sound waves to identify inner defects, giving an extensive analysis of weld honesty. Radiographic testing utilizes X-rays or gamma rays to produce photos of the weld, revealing internal defects that are not visible to the naked eye.
Magnetic fragment testing is specifically reliable for ferromagnetic products, recognizing surface area and near-surface problems by applying electromagnetic fields and utilizing great bits that indicate abnormalities. Dye penetrant testing entails using a tinted color to the weld surface, which permeates right into cracks and is disclosed under ultraviolet light, making it easy to identify problems.
Each of these methods plays an important duty in maintaining welding top quality, and the selection of a suitable approach depends upon the certain requirements of the fabrication task, consisting of product kind, weld setup, and the desired degree of evaluation.
Vital Examination Tools
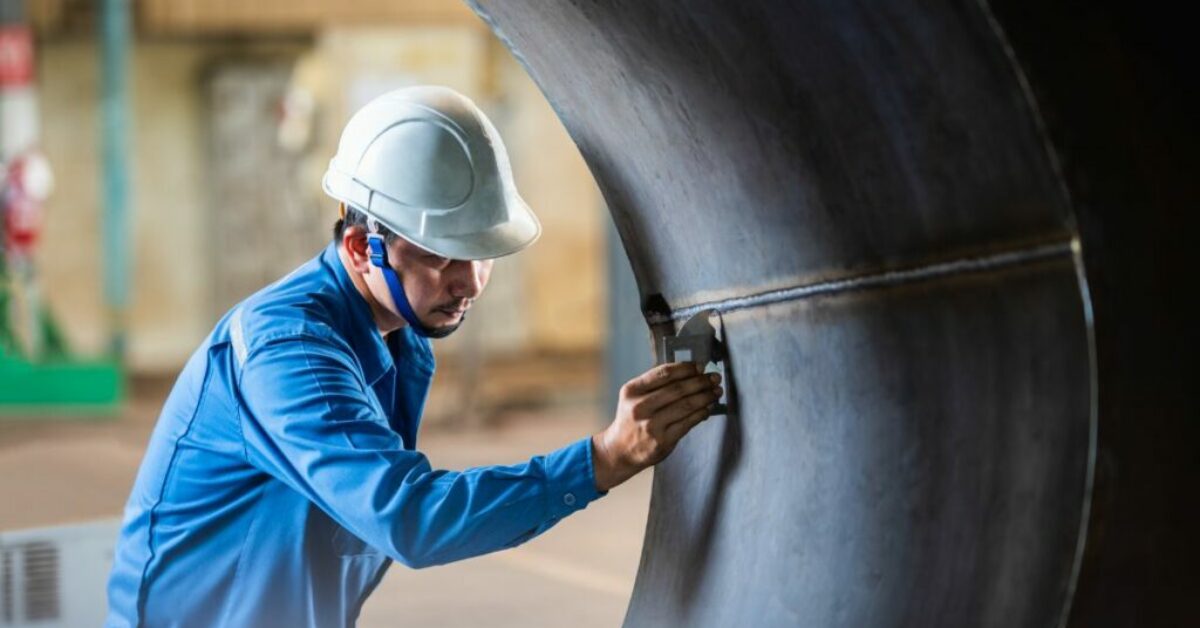
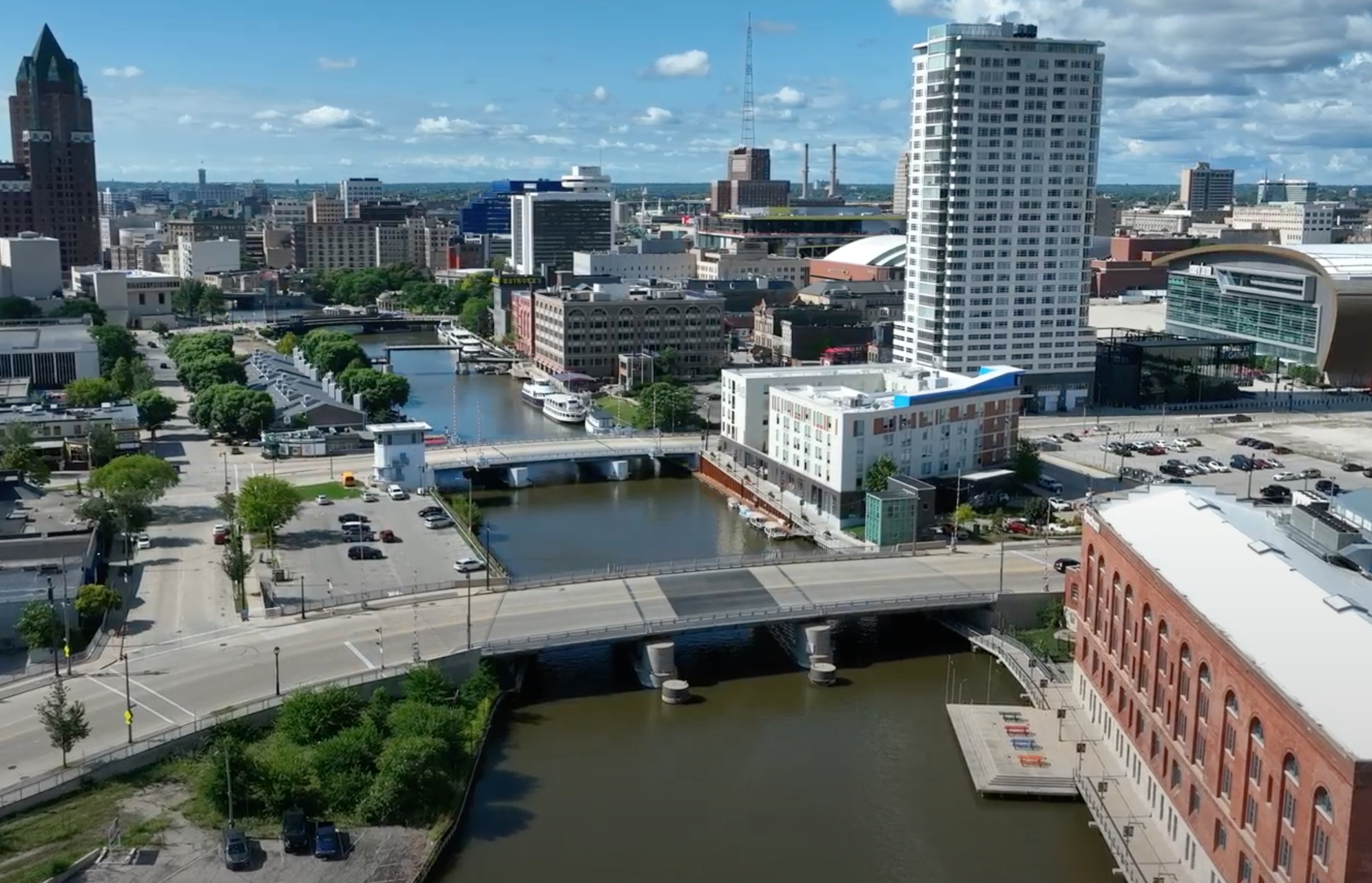
Gauging devices, consisting of calipers, evaluates, and leaders, are vital for validating dimensions and tolerances. These instruments assist guarantee that welds fulfill the needed requirements for toughness and toughness. Furthermore, ultrasonic screening devices are used to find internal problems without endangering the integrity of the weld. This non-destructive screening approach is vital for identifying issues that may not be visible on the surface.
Another important device is the hardness tester, which assesses the mechanical properties of a weld and determines its viability for details applications. Ultimately, welding examination software program aids in documenting searchings for, promoting data evaluation, and making certain compliance with industry criteria. Together, these essential assessment tools develop a thorough toolbox that supports the welding examination process, inevitably adding to the quality assurance of manufacture projects.
Best Practices for Top Quality Assurance
In the search of top quality guarantee, applying ideal techniques is important for accomplishing reputable and constant welding results. Developing a thorough welding high quality monitoring system (WQMS) is fundamental. This system must encompass defined treatments, standards, and paperwork practices that guide every stage of the welding process.
Routine training and certification of welding workers are important. Proficient welders with upgraded understanding of techniques and safety and security actions add significantly to high quality. Conducting pre-welding assessments makes sure that materials and devices fulfill specified requirements, reducing the likelihood of flaws.
Incorporating real-time surveillance throughout the welding procedure enables prompt discovery of abnormalities, allowing restorative activities to be taken without delay. Post-welding inspections, consisting of visual checks and non-destructive testing (NDT), are vital in validating weld integrity and compliance with industry requirements.
Additionally, keeping precise records of inspections, weld criteria, and rehabilitative actions fosters a culture of accountability and constant improvement. Involving stakeholders in normal high quality reviews can likewise enhance the overall efficiency of quality control procedures. By sticking to these finest methods, organizations can considerably elevate their welding quality control efforts, therefore making sure project success and client contentment.
Enhancing Safety And Security and Conformity
Achieving high requirements in welding top quality guarantee naturally straightens with the necessary of improving helpful resources security and compliance within the market. Effective welding examination techniques are important in determining prospective risks and making certain that all procedures stick to regulatory standards. These strategies not just offer to preserve structural honesty yet additionally protect the wellness and security of employees associated with manufacture tasks.
Applying extensive assessment methods, such as visual assessments, non-destructive testing (NDT), and thorough documents, develops a society of safety and accountability. Educating welders and assessors in current safety guidelines and finest techniques is vital. This guarantees that all staff member know potential risks and are outfitted to reduce them.
Moreover, conformity with industry criteria, such as those set by the Recommended Reading American Welding Society (AWS) and the International Organization for Standardization (ISO), is non-negotiable. Routine audits and analyses help determine spaces in safety and security actions and promote continuous enhancement - Welding Inspection Milwaukee. Eventually, a commitment to improving security and conformity not just fosters a more secure working environment however also brings about exceptional top quality outcomes and minimized responsibility for companies engaged in welding manufacture
Conclusion
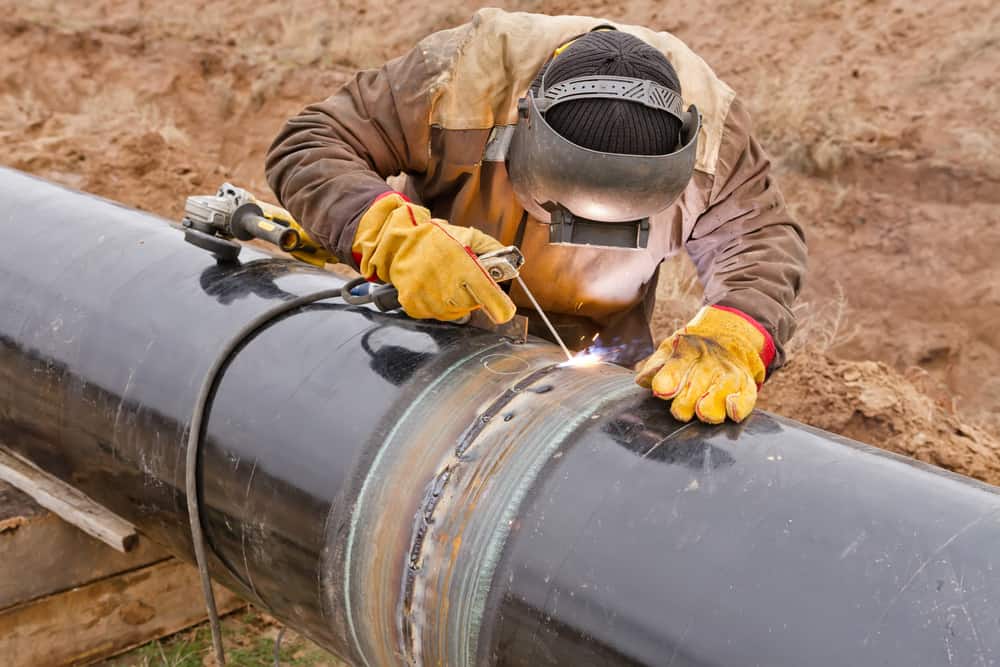
Welding evaluation serves as a fundamental pillar in guaranteeing the structural honesty and safety of made tasks.Welding inspection is an essential part in making sure the stability and safety and security of bonded structures. Ultimately, focusing on welding inspection promotes a society of top quality guarantee, making sure that jobs fulfill both customer assumptions and governing demands. Together, these vital examination tools create a detailed toolbox that supports the welding assessment process, ultimately adding to the high quality guarantee of manufacture projects.
In conclusion, efficient Clicking Here welding assessment is critical for ensuring the architectural honesty and security of fabricated jobs. Welding Inspection Milwaukee.